Scraper Conveyor
Used for the removal of swarf from machine tools or incorporated into a central system.
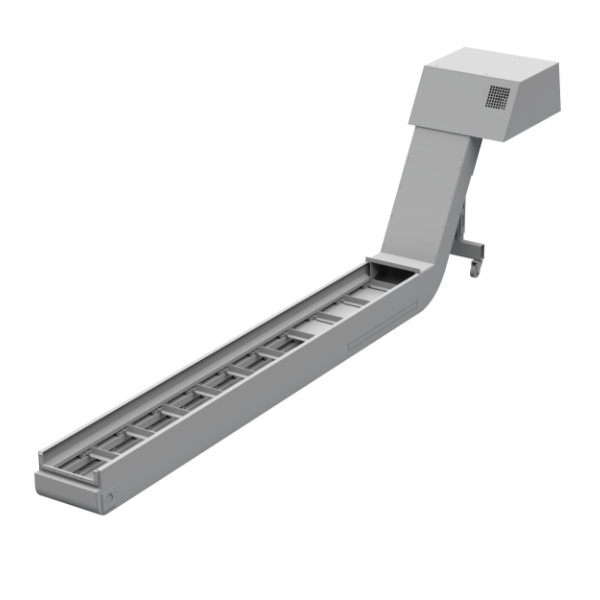
How it works
Chipped swarf drops into the case guided by chuting. The swarf is dragged towards the discharge point through the closed contact between the scraper bar and the bottom of the conveyor case. This is driven by an externally mounted motor, assembled with direct drive or an optional variable speed drive.
A further option of a slipping clutch type drive is available with a top mounted motor arrangement. This option assists with conveyor jams, as it protects the conveyor and gearbox. For applications where coolant is present, the scraper conveyor can include first stage filtration. This consists of a wedge wire filter box located in the case positioned within the belt loop. This is self-cleaning, as the belt returns from the discharge point, brushes attached to the back of interval scraper bars brush the wedge wire filter box clean.
Additional information
1. Extra Filter boxes for increased flow
2. Discharge height
3. Colour
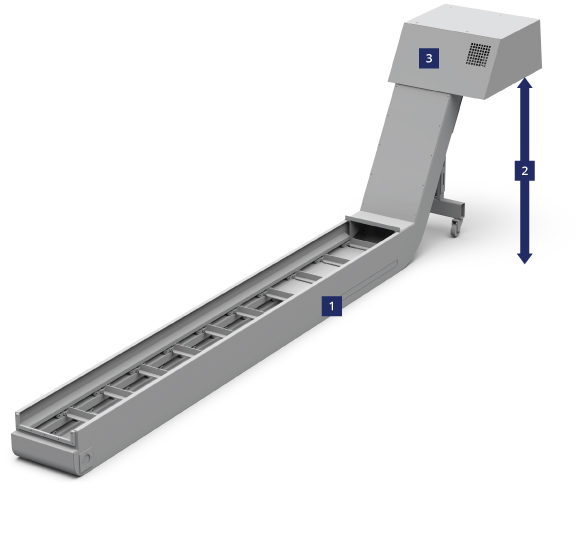
Features and Benefits
- Designed specifically to handle chipped swarf (Brass, Aluminium, Cast)
- Robust construction
- Reliable and long-term performance
- Designed to suit existing machine tank
- Plug and play
- Maintenance friendly
- Bespoke options (discharge height +/-)
Principal Applications
- Horizontal machining centres
- Vertical machining centres
- Multi-tasking machine
- CNC turning centres
- Special purpose machine tools
- Linked to central conveyor systems
- Underground swarf handling
- Suitable for handling chipped swarf only;
- Aluminium, brass, cast iron, wet and dry
- Swarf Processing
Suitable Swarf Types
Suitable for handling the following swarf types:
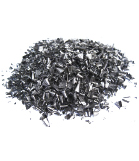
Small Chipped Swarf
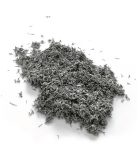
Fine Swarf
Get in touch
Please fill out the form below and our team will be in touch